Three separation methods are predominant for separating constituent gases from the air. They are:
- Membrane separation
- Pressure swing adsorption
- Low-temperature rectification, or cryogenic distillation process
Membrane Separation:
In this separation process, equipment pumps air into the membrane module and the targeted gases like oxygen and nitrogen are separated based on differences in diffusivity and solubility. For example, oxygen can be separated from the ambient air and collected at the upstream side, and nitrogen at the downstream side.
In this separation process, equipment pumps air into the membrane module and the targeted gases like oxygen and nitrogen are separated based on differences in diffusivity and solubility. For example, oxygen can be separated from the ambient air and collected at the upstream side, and nitrogen at the downstream side.
Pressure Swing Adsorption:
The principle of Pressure Swing Adsorption (PSA) is the amount of adsorbate deposited on the adsorbent increases with increasing pressure. Adsorption increase with increasing pressure, desorption occurs at low pressure. The technique is applied for the adsorptive recovery of O2 and N2 from the air.
The principle of Pressure Swing Adsorption (PSA) is the amount of adsorbate deposited on the adsorbent increases with increasing pressure. Adsorption increase with increasing pressure, desorption occurs at low pressure. The technique is applied for the adsorptive recovery of O2 and N2 from the air.
Cryogenic Air Separation:
A cryogenic air separation unit (ASU) is a process plant in which air is separated into its component gases by distillation at low temperatures.
The plant comprises an assembly of equipment like distillation columns, heat exchangers, adsorbers, and supporting machinery for compression, expansion, and control of gases
and liquids. The component gases are sold and distributed to customers for a wide variety of industrial, medical, and other specialist applications as per requirement. Air separation plants are constructed in different forms depending on what products are produced and production capacity and purity requirement by the client. Moreover process equipment and machinery from different manufacturers are used as per requirement. However, the basic principles of construction and operating methods for all these different plants are nearly the same.
The design of a cryogenic air separation plant depends on the scale of operations and the nature of the products required from it. While basic principles are always the same, process cycles and flow for each plant can vary significantly based on the requirement.
Air separation plants operate on a range of different process cycles to meet specific customer requirements, in a range of plant capacities extending to the production of over 2,300 tones per day of oxygen, with co-production of nitrogen and argon and sometimes krypton and xenon.
and liquids. The component gases are sold and distributed to customers for a wide variety of industrial, medical, and other specialist applications as per requirement. Air separation plants are constructed in different forms depending on what products are produced and production capacity and purity requirement by the client. Moreover process equipment and machinery from different manufacturers are used as per requirement. However, the basic principles of construction and operating methods for all these different plants are nearly the same.
The design of a cryogenic air separation plant depends on the scale of operations and the nature of the products required from it. While basic principles are always the same, process cycles and flow for each plant can vary significantly based on the requirement.
Air separation plants operate on a range of different process cycles to meet specific customer requirements, in a range of plant capacities extending to the production of over 2,300 tones per day of oxygen, with co-production of nitrogen and argon and sometimes krypton and xenon.
Process overview of Cryogenic Air Separation Plant:
The basic process for large-scale air separation has remained unchanged for decades but the orientation of equipment will change based on process requirements. In this process, the air is compressed, then purified by removing carbon dioxide and water vapor, after that dried and cleaned air is cooled to nearly its liquefaction temperature, and then separated by cryogenic distillation into oxygen, nitrogen, and argon products.
Importance of cryogenic air separation:
Cryogenic air separation technology has the ability to produce the largest capacities of products at a high-purity level, compared to non-cryogenic based systems such as pressure-swing adsorption and membrane technologies, which are employed at the lower end of production scale and low purities.
Products of Cryogenic Air Separation Plant:
Product names are LOX (Liquid Oxygen), LIN (Liquid Nitrogen), LAR (Liquid Argon), GOX (Gaseous Oxygen), and GAN (Gaseous Nitrogen).
Product names are LOX (Liquid Oxygen), LIN (Liquid Nitrogen), LAR (Liquid Argon), GOX (Gaseous Oxygen), and GAN (Gaseous Nitrogen).
In the case of large LOX (and LIN) production, a separate liquefier may exist with a permanent liquid assist from liquefier (for storage, when liquefier is stopped).
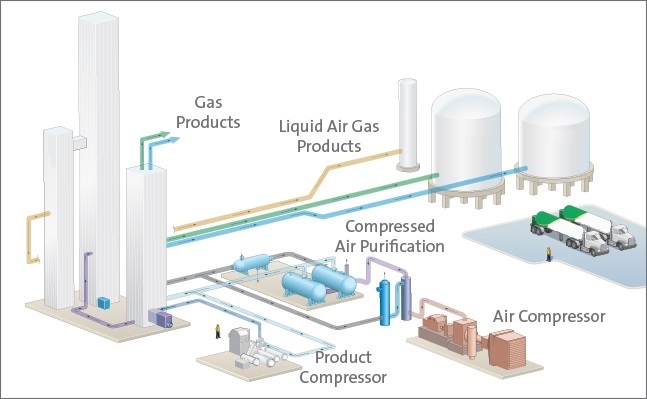